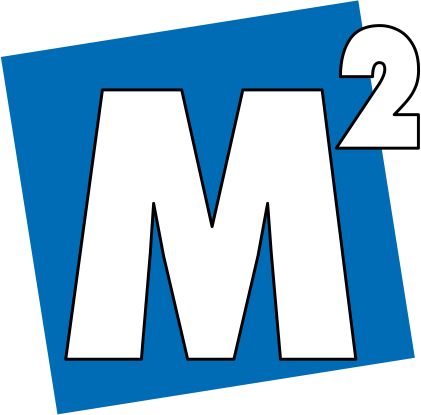
Техобслуживание, модернизация станков, в т.ч. с ЧПУ
200 000 руб.,
Москва | Добавлено: 14 июля 2017, номер: 8802
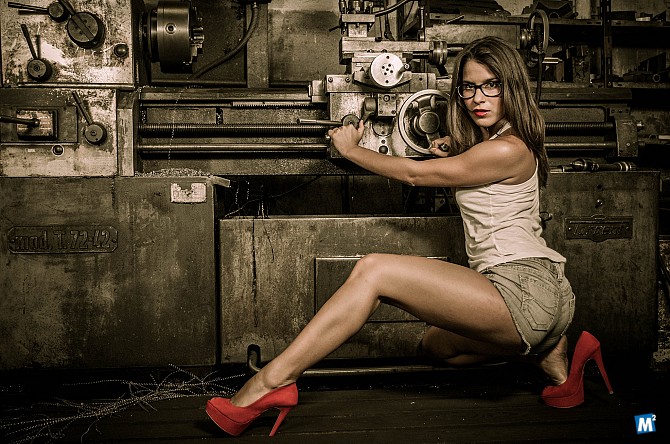
Адрес: Москва,
Так же мы оказываем услуги по оценке технического состояния металлоредущих станков и кузнечно-прессового оборудования, его ремонтопригодности, с составлением деффектовочной ведомости. Производим текущий и средний ремонт станков.
Работы выполняемые при диагностике, техническом обслуживании и текущем ремонте станков
1. Наружный осмотр без разборки для выявления дефектов, состояния и работы станка (машины) в целом.
2. Промывка, протирка направляющих станка, смазка маслом всех поверхностей.
3. Проверка правильности переключения рукояток скоростей и подач. Необходимая регулировка по результатам проверки.
4. Проверка правильности переключения и исполнения команд, поданных с пульта управления (для станков с ЧПУ).
5. Проверка работы на всех режимах резания (на холостом ходу).
6. Осмотр состояния направляющих кареток, траверс и других трущихся поверхностей.
7. Подтяжка ослабленных крепежных деталей. Проведение необходимых регулировок.
8. Подтяжка ослабленных крепежных деталей валов, ходовых винтов. Проведение необходимых регулировок.
9. Проверка исправности действия ограничителей, переключателей, упоров и других автоматических устройств.
10. Проверка натяжения ремней. Проведение необходимых регулировок.
11. Проверка наличия и исправности оградительных устройств (предохранительных щитков, кожухов и др.).
12. Проверка отсутствия вибрации узлов оборудования. При необходимости проведение регулировок.
13. Проверка уровня шума оборудования.
14. Проверка нагрева подшипников. По результатам проверки – регулировка натяжения или составление акта о необходимости замены.
15. Проверка усилия зажима и состояния зажимного патрона.
16. Проверка зажима резцетержателя режущего инструмента.
17. Проверка состояния смазочных систем (отсутствие течи масла, уровень масла по указателю, отсутствие ударов при работе гидросистем, рывков при реверсировании). По результатам проверки проведение необходимых регулировок или необходимых работ по устранению течи.
18. Проверка исправности действия фрикционов. Проведение необходимых регулировок.
19. Проверка исправности действия тормозов. Регулировка.
20. Проверка плавности перемещения столов, суппортов, кареток, ползунов.
21. Проверка и подтяжка клиньев суппортов, кареток.
22. Проверка и подтяжка прижимных планок всех узлов станка.
23. Зачистка забоин, царапин, задиров на направляющих станины, кареток, траверс и на других трущихся поверхностях.
24. Проверка натяжения пружин (при наличии) их подтяжка, зачистка или замена ослабленных или изношенных крепежных деталей (шпилек, гаек, винтов и др.).
25. Проверка состояния системы охлаждения. Проведение текущего ремонта.
26. Проверка и регулирование зазоров винтовых пар.
27. Проверка и регулирование подшипников шпинделя.
28. Замена смазочных материалов (каждые 750 часов работы или согласовывается с заказчиком).
Работы включают в себя:
► Слив отработанного масла.
► Очистка емкостей системы от осадков, грязи и остатков масла.
► Проверка, чистка масляных фильтров.
► Протирка емкостей и корпусов салфетками без ворса.
► Заливка резервуара маслом.
► Точечное заполнение мест смазки согласно карте смазки (выполняется при каждом ТО).
29. Проверка основных параметров технологической точности (проверка готовности к производству деталей с необходимой точностью) не реже - раз в 6 месяцев. По результатам проверок по каждой единице оборудования Заказчику предоставляется акт с указанием проверок, отклонений и методов их устранения.
30. Своевременное составление спецификаций на приобретение или изготовление запасных частей, необходимых для проведения текущего ремонта и закупки расходных материалов для проведения ТО.
* По согласованию сторон закупку, согласно составленных спецификаций, может производить Исполнитель за дополнительную плату.
Техническое обслуживание электрической части станков включает в себя следующие работы:
31. Проверка кнопок аварийной остановки каждого с
Работы выполняемые при диагностике, техническом обслуживании и текущем ремонте станков
1. Наружный осмотр без разборки для выявления дефектов, состояния и работы станка (машины) в целом.
2. Промывка, протирка направляющих станка, смазка маслом всех поверхностей.
3. Проверка правильности переключения рукояток скоростей и подач. Необходимая регулировка по результатам проверки.
4. Проверка правильности переключения и исполнения команд, поданных с пульта управления (для станков с ЧПУ).
5. Проверка работы на всех режимах резания (на холостом ходу).
6. Осмотр состояния направляющих кареток, траверс и других трущихся поверхностей.
7. Подтяжка ослабленных крепежных деталей. Проведение необходимых регулировок.
8. Подтяжка ослабленных крепежных деталей валов, ходовых винтов. Проведение необходимых регулировок.
9. Проверка исправности действия ограничителей, переключателей, упоров и других автоматических устройств.
10. Проверка натяжения ремней. Проведение необходимых регулировок.
11. Проверка наличия и исправности оградительных устройств (предохранительных щитков, кожухов и др.).
12. Проверка отсутствия вибрации узлов оборудования. При необходимости проведение регулировок.
13. Проверка уровня шума оборудования.
14. Проверка нагрева подшипников. По результатам проверки – регулировка натяжения или составление акта о необходимости замены.
15. Проверка усилия зажима и состояния зажимного патрона.
16. Проверка зажима резцетержателя режущего инструмента.
17. Проверка состояния смазочных систем (отсутствие течи масла, уровень масла по указателю, отсутствие ударов при работе гидросистем, рывков при реверсировании). По результатам проверки проведение необходимых регулировок или необходимых работ по устранению течи.
18. Проверка исправности действия фрикционов. Проведение необходимых регулировок.
19. Проверка исправности действия тормозов. Регулировка.
20. Проверка плавности перемещения столов, суппортов, кареток, ползунов.
21. Проверка и подтяжка клиньев суппортов, кареток.
22. Проверка и подтяжка прижимных планок всех узлов станка.
23. Зачистка забоин, царапин, задиров на направляющих станины, кареток, траверс и на других трущихся поверхностях.
24. Проверка натяжения пружин (при наличии) их подтяжка, зачистка или замена ослабленных или изношенных крепежных деталей (шпилек, гаек, винтов и др.).
25. Проверка состояния системы охлаждения. Проведение текущего ремонта.
26. Проверка и регулирование зазоров винтовых пар.
27. Проверка и регулирование подшипников шпинделя.
28. Замена смазочных материалов (каждые 750 часов работы или согласовывается с заказчиком).
Работы включают в себя:
► Слив отработанного масла.
► Очистка емкостей системы от осадков, грязи и остатков масла.
► Проверка, чистка масляных фильтров.
► Протирка емкостей и корпусов салфетками без ворса.
► Заливка резервуара маслом.
► Точечное заполнение мест смазки согласно карте смазки (выполняется при каждом ТО).
29. Проверка основных параметров технологической точности (проверка готовности к производству деталей с необходимой точностью) не реже - раз в 6 месяцев. По результатам проверок по каждой единице оборудования Заказчику предоставляется акт с указанием проверок, отклонений и методов их устранения.
30. Своевременное составление спецификаций на приобретение или изготовление запасных частей, необходимых для проведения текущего ремонта и закупки расходных материалов для проведения ТО.
* По согласованию сторон закупку, согласно составленных спецификаций, может производить Исполнитель за дополнительную плату.
Техническое обслуживание электрической части станков включает в себя следующие работы:
31. Проверка кнопок аварийной остановки каждого с